What is the Difference Between CNC and Sheet Metal Fabrication?
In modern manufacturing, CNC machining and sheet metal fabrication are two widely used processes for producing metal components. While both techniques involve shaping and processing metal, they serve different purposes, utilize distinct methodologies, and are suited for specific applications. As a manufacturer, understanding the differences between CNC machining and sheet metal fabrication is crucial for selecting the right process to optimize production, ensure cost-effectiveness, and meet quality standards. In this article, we will explore the key differences between CNC and sheet metal fabrication, helping procurement professionals make informed purchasing decisions.
1. Understanding CNC Machining
CNC (Computer Numerical Control) machining is a subtractive manufacturing process that uses computer-controlled tools to remove material from a solid workpiece. This technique is widely used for creating precise, complex, and high-tolerance components across various industries.
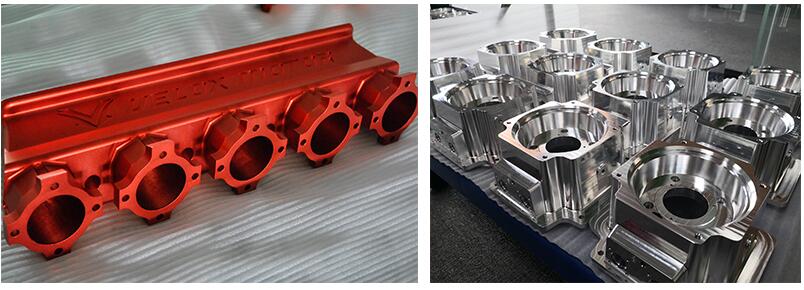
Key Features of CNC Machining:
- High Precision: CNC machines can achieve tolerances as tight as ±0.001 inches, making them ideal for aerospace, medical, and automotive applications.
- Versatile Materials: CNC machining works with metals such as aluminum, steel, titanium, and copper, as well as plastics and composites.
- Automated Production: Computer-controlled operations ensure consistency, repeatability, and reduced human error.
- Complex Geometries: CNC allows for intricate designs, including 3D contours and detailed engraving.
- Cost Consideration: Higher initial costs due to machine setup, but cost-efficient for low to medium production runs requiring precision.
2. Understanding Sheet Metal Fabrication
Sheet metal fabrication involves forming, cutting, and assembling flat sheets of metal into desired shapes and structures. Unlike CNC machining, which removes material, sheet metal fabrication reshapes and joins metal parts to create durable components.
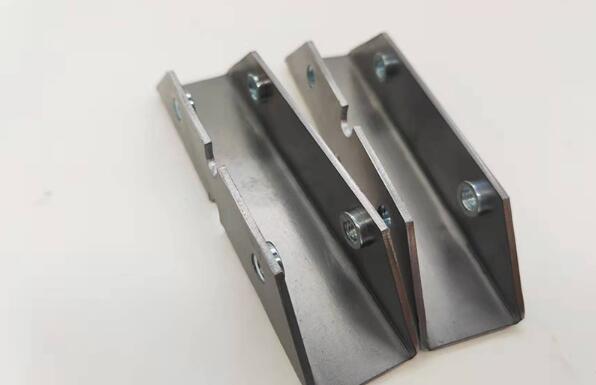
Key Features of Sheet Metal Fabrication:
- Material Efficiency: Fabrication minimizes material waste by reshaping rather than cutting away excess material.
- Cost-Effective for Large Volumes: Best suited for high-volume production due to lower material costs and fast manufacturing processes.
- High Strength and Durability: Used for creating structural and functional parts in industries such as construction, electronics, and HVAC.
- Processes Involved: Includes cutting (laser cutting, waterjet cutting), bending, stamping, welding, and coating.
- Customizable Designs: Suitable for large enclosures, brackets, housings, and architectural structures.
3. Key Differences Between CNC Machining and Sheet Metal Fabrication
Feature | CNC Machining | Sheet Metal Fabrication |
---|---|---|
Material Usage | Subtractive process (removes material) | Forming and joining processes |
Precision & Tolerance | High precision (±0.001 inches) | Lower tolerance compared to CNC machining |
Best for | Small, intricate, and complex parts | Large, structural, and enclosures |
Material Waste | Generates more waste due to cutting | More material-efficient |
Production Volume | Best for low to medium production | Ideal for high-volume production |
Cost Consideration | Higher initial costs; expensive for large runs | More cost-effective for bulk production |
4. Applications of CNC Machining vs. Sheet Metal Fabrication
When to Choose CNC Machining:
- High-precision components for aerospace and medical industries.
- Complex parts with detailed geometries.
- Small production batches requiring superior accuracy.
- Custom one-off parts and prototypes.
When to Choose Sheet Metal Fabrication:
- Large-scale production of enclosures, cabinets, and panels.
- Durable parts for industrial and construction applications.
- Cost-effective mass production of standard metal parts.
- Components requiring bending, stamping, or welding.
5. Choosing the Right Manufacturing Process
Selecting between CNC machining and sheet metal fabrication depends on several factors, including the complexity of the design, material considerations, production volume, and budget constraints. A reputable manufacturer can guide businesses toward the most efficient and cost-effective method based on project requirements.
Conclusion
While CNC machining and sheet metal fabrication both play vital roles in modern manufacturing, they cater to different needs. CNC machining excels in producing highly precise, intricate parts, while sheet metal fabrication is the go-to choice for durable, large-scale components. Understanding these differences helps manufacturers and procurement professionals optimize production, reduce costs, and ensure high-quality output. Partnering with an experienced supplier ensures that businesses get the best solution tailored to their specific industry requirements.